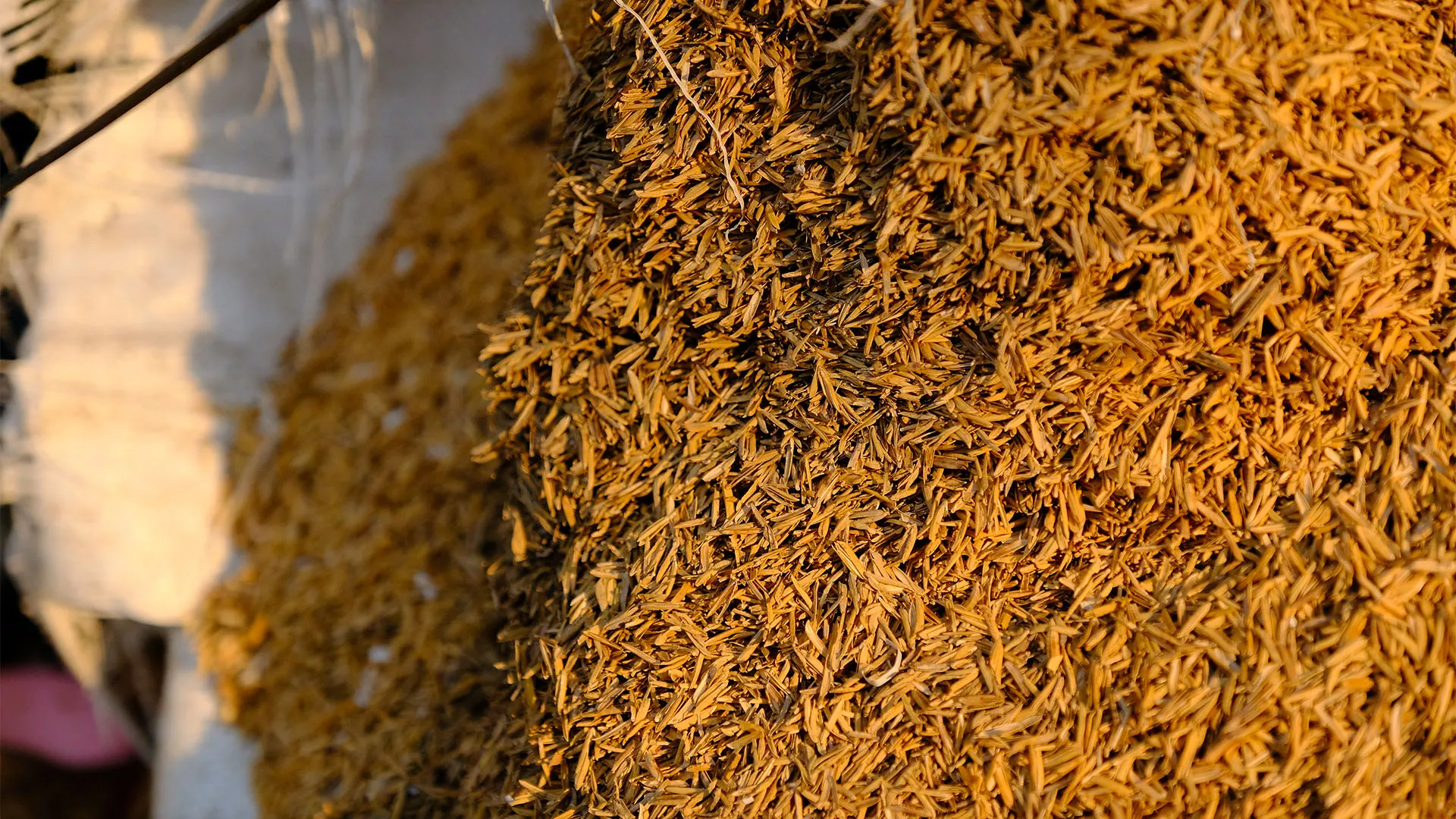
Reinventing materials, building tomorrow
One example of a bio- based material is rice husk. The outer layer of the rice grain, rice husk has strong insulating properties and is also resistant to rot, which makes it particularly suitable for insulating buildings.
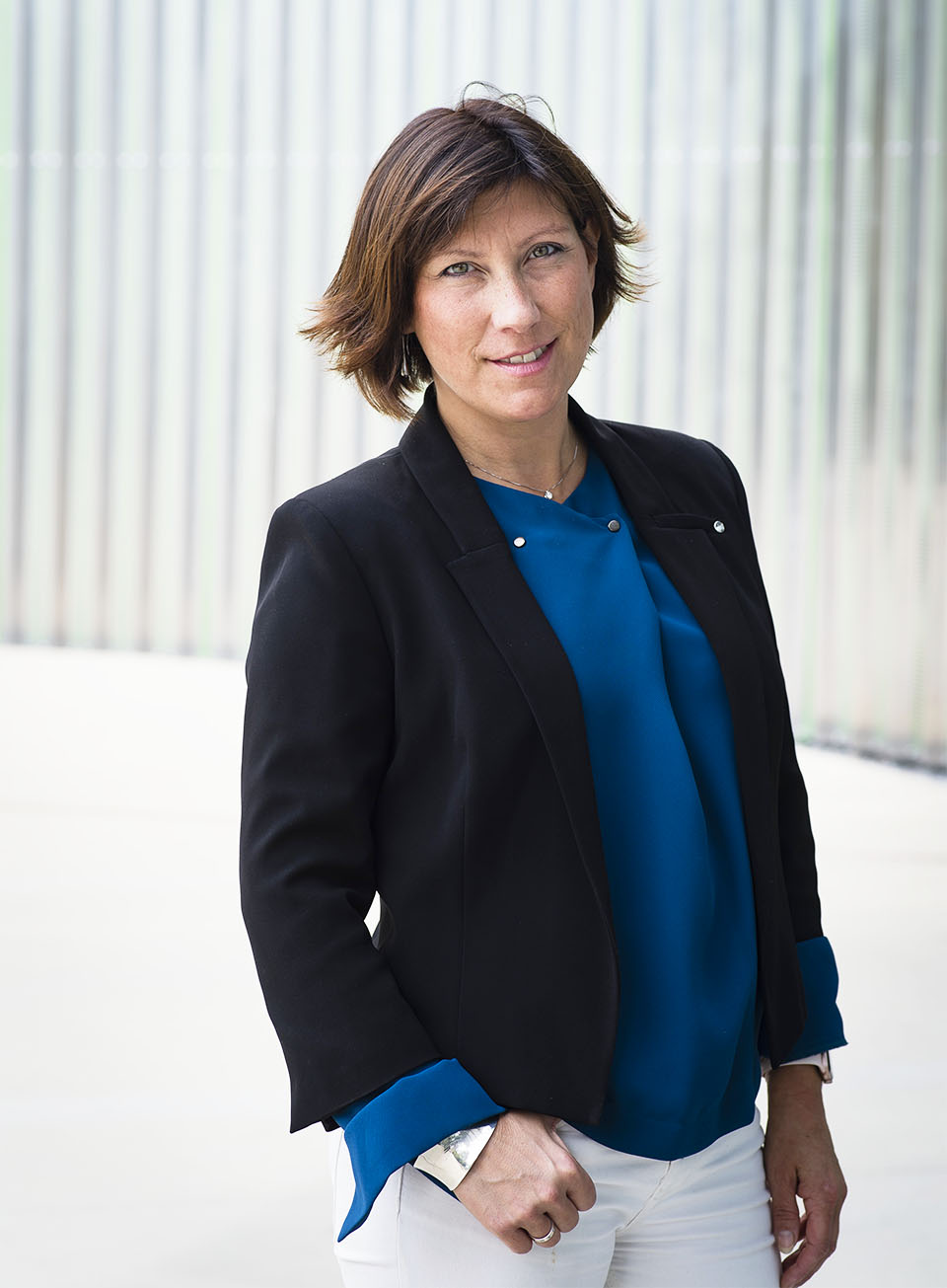
Céline Perlot-Bascoulès
Teacher - researcher at ISA BTP1, head of the Geomaterials and Civil Engineering Structures team at the SIAME laboratory2, junior member of the Institut Universitaire de France.
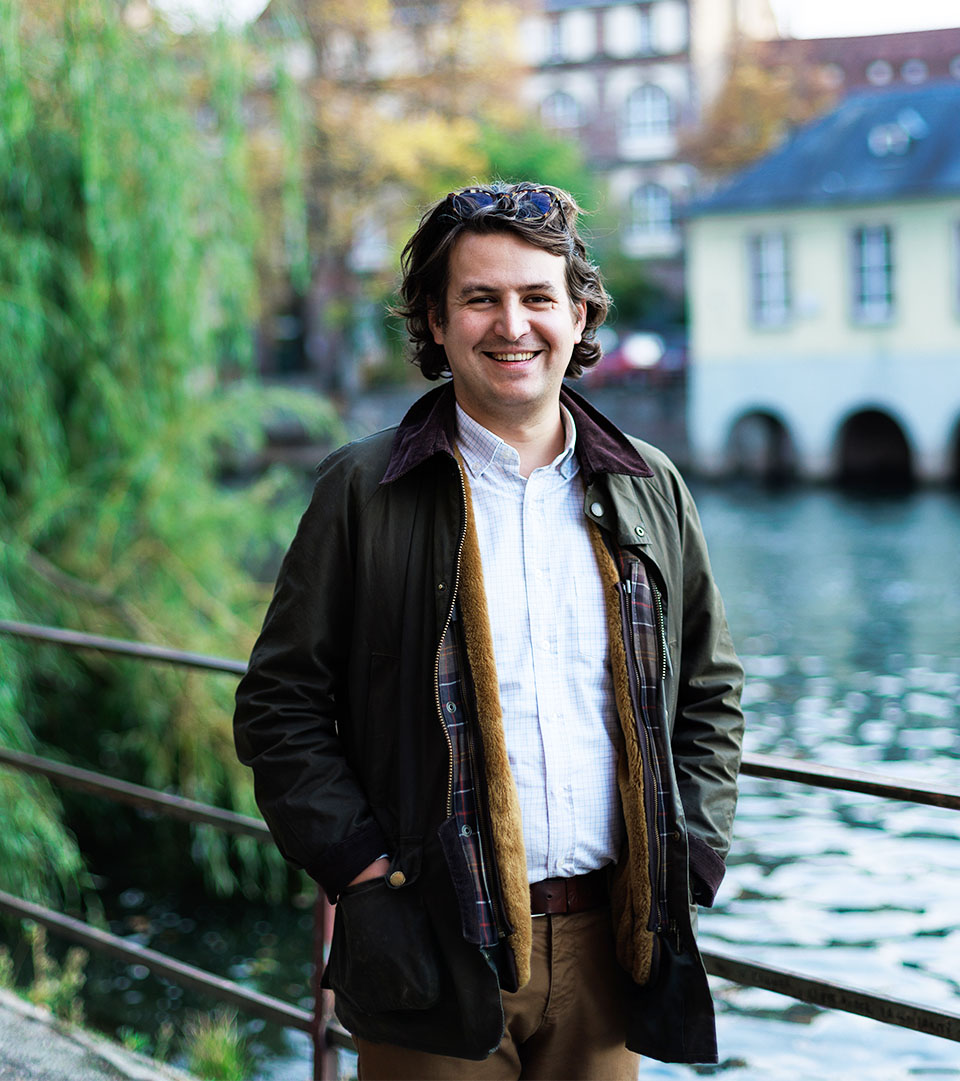
Laurent Fehr
FEHR Group development director3, Alsatian family company specialised in concrete solutions.
What is the best way to meet the challenge of the ecological and climate transition and build tomorrow’s low environmental impact buildings?4
Céline Perlot-Bascoulès: It is notable that in the building sector, we are now speaking of ecological transition and no longer just energy, as witnessed by the new French regulation RE20205 . Beyond energy— the so-called ‘grey’ energy used during the manufacture of materials and used in the operation of a building — the sector is now concerned with the complete set of environmental impacts it is responsible for such as waste management and the depletion of natural resources, air and water pollution, biodiversity, and the comfort and health of users. Research is certainly intensifying in these areas. As an example, our laboratory works on the quality of air in buildings, an important subject when you consider that we spend more than 90% of our time inside. This research is leading us to develop raw earth-based materials capable of retaining indoor pollutants. That said, the miracle recipe for low-impact building does not yet exist because each development project is unique. Nonetheless, it is above all about using the right materials in the right place for the right end-use, in line with the needs of the users.
Lawrence Fehr: We should highlight four points. Materials first. We must decarbonise their manufacturing processes, favouring local resources, moving towards increased diversity in their use because it is the performance of different materials that will make a building clean and sustainable over time.
After that comes the collaborative work between architecture and engineering through the use of digital tools. The BIM approach (Building Information Modelling), for example, makes it possible to consider all the stages of construction using a digital model. This will help improve the performance of the construction site by avoiding errors and waste. I can imagine the future of construction as similar to that of the automobile, where buildings will no longer be built on site but will be assembled on the basis of prefabricated elements. The RE2020 standard is an essential starting point and creates real dynamism in the sector. As the Shift Project points out6, France can become a global laboratory for green concrete construction. This regulation must go even further in terms of sustainability — imposing sustainable constructions that last over at least a hundred years seems essential to me — and also reversibility. This is because being able to change the end-use of a building (housing, offices, workshops, etc.) makes it inherently more sustainable. Finally, we must learn to be collectively more restrained in our use of land and living space. Increasing the density of habitation and use of cities is one solution, provided of course we make them pleasant to live in.
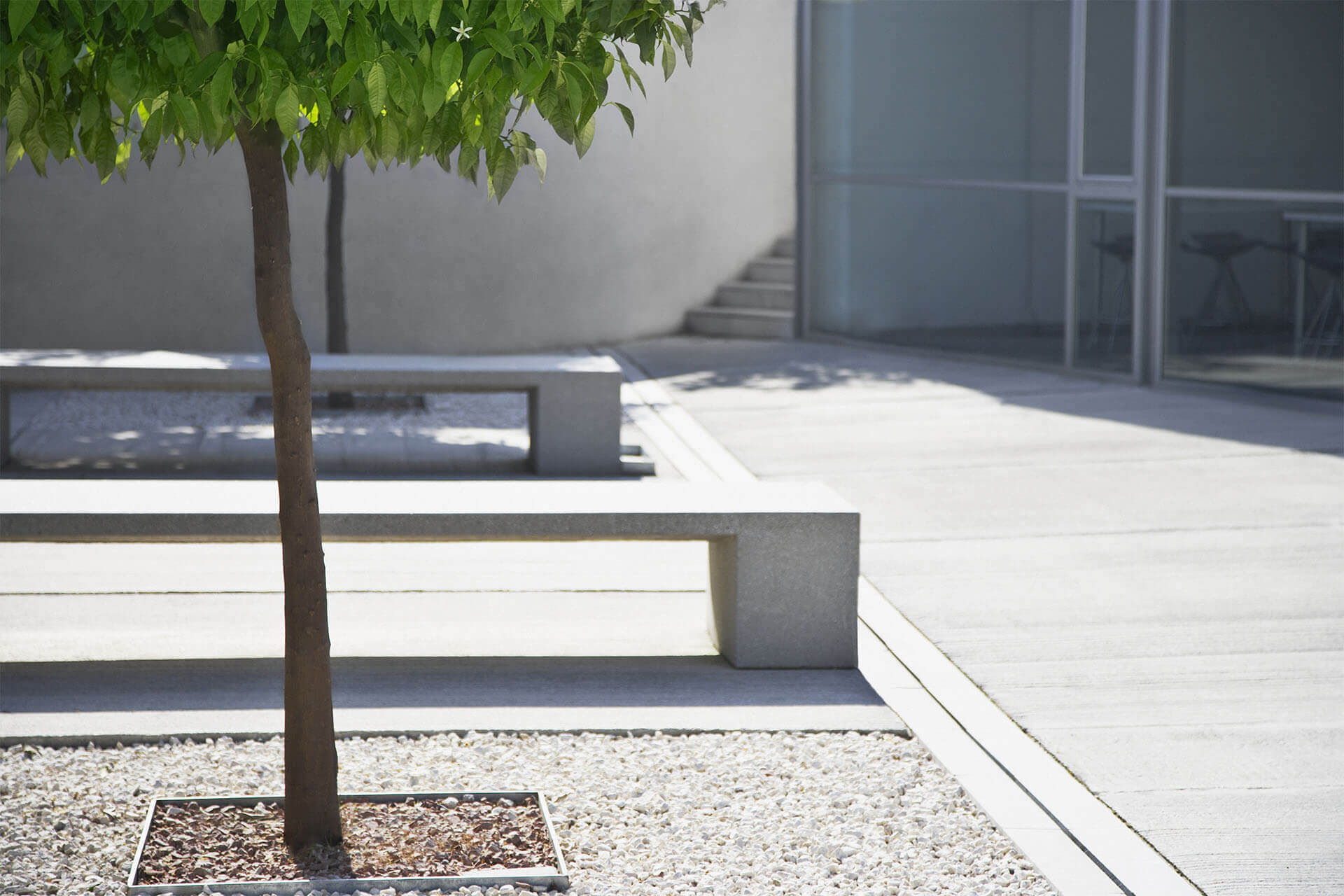
In city centres, new materials could reduce the phenomenon of urban heat islands caused by the use of concrete-type materials which absorb heat and release it slowly at night.
What are the new materials that will be used in the clean construction of tomorrow?
CP-B: In reality, the new materials we are talking about today are not new at all! Straw or earth, for example, have been used for a very long time. But there is a revival of these so-called bio-based and geo-based materials7, along with the desire to identify local sources. For example, these will include agricultural by-products - hemp fibres, straw, sunflower pith8 — which will serve as thermal insulators instead of petrochemical products. Research thus calls for an interdisciplinary approach, bringing together engineering sciences, biology and agronomy. Raw earth is experiencing a strong resurgence of interest, as shown by the ‘National EARTH Project’ launched in 2021. This material has the advantage of being available locally and in quantity, of having low grey energy cost and of exhibiting hygrothermal regulation and thermal inertia properties. Our research focuses, for example, on the development of zero-carbon panels with a wooden frame: compressed raw earth without chemical binders, with the addition of sheep’s wool9 (for strength) for use in facing, replacing the usual bricks and plasterboard. Sunflower pith could complete the insulation for the panel.
This project is illustrative of a multi-material approach that will be developed in construction. The SIAME laboratory helps co-pilot a RILEM research group10 on the development of alternative bio-stabilisers to cement, based on natural products (mushrooms, tannins, agro-food residues, etc.) in order to strengthen the mechanical resistance and durability of raw earth. International research cooperation helps researchers share knowledge on these bio and geo-sourced materials for which we still currently lack data, characterisations and standards that would make it possible to improve them even further.
LF: I strongly believe in the development of these low carbon footprint, bio-based and geo-based materials. Our company relies on natural materials such as straw, hemp or raw earth. For example, we created around thirty interior walls in raw earth, with a wooden frame and straw for the binder, for the James Baldwin media library in Paris, designed by the architect Philippe Madec.
The use of raw earth helps regulate the humidity level of the air, contributing to the energy performance of the building. And it is a real alternative to high-carbon materials used for partitioning such as plaster and steel. The key to ecological construction is indeed to use the right material in the right location while taking into account the specificities of each territory. The most widely used today, such as concrete in particular, will keep their place but will be more and more combined with organic and geosourced materials.
Is concrete, whose production is very carbon-intensive, reinventing itself?
LF: I am convinced that concrete11, once the path to decarbonisation has been completed, will be a true ally of the ecological transition! But to do this, we must above all decarbonise the production of cement, which generates 98% of the CO2 emissions of concrete. This involves lowering the levels of clinker12 in cement and through the use of non-fossil fuels. Cement manufacturers are moving in this direction in offering new, low-carbon cements and the RE2020 regulations strongly encourage them to do so. The work on construction design is also very important in decreasing concrete use and that of other materials. The use of recycled aggregates, resulting from the demolition of old buildings, is also a way that FEHR Group privileges. This circular economy makes it possible to use less sand and gravel, preserving these natural resources, even if certain regions such as Alsace have them in abundance. Above all, innovation contributes to the development of low-carbon solutions. For example, the company has developed a double wall using 100% recyclable exterior thermal insulation for new construction. Précoffré TH® Green is made from low-carbon concrete (recycled aggregates and low-carbon cement) with biosourced insulation (wood fibre) and an integrated window to guarantee maximum air-and- water-tightness. On the renovation market, we have developed an unprecedented construction solution using ultra-high performance concrete and wooden frame walls. This results in the volume of concrete used being divided by ten compared to standard concrete while also offering a facade curtain wall that is low-carbon too.
CP-B: A new generation of cements is now coming to the market with a reduced carbon footprint of between 70 to 80% compared to traditional cement. The use of recycled aggregates from the demolition of buildings is another area that must be developed. Countries such as Denmark, the Netherlands, Norway, Germany and Switzerland are well on their way down this path. The recycling of industrial by-products as substitutes for aggregates is also an important route to take: for example, the laboratory is carrying out a research project with the University of Navarre, in Spain, to recover steelworks slag. In another example, as part of a partnership with the Arcachon basin shellfish farming union and the LFC-R laboratory, we are experimenting with the use of crushed oyster shells as a substitute for aggregates. These approaches help limit the environmental footprint of concretes. Much research is also focused on their new uses. At SIAME, we are trying to develop a very porous concrete, capable of storing rainwater and cooling the atmosphere by evapotranspiration. Used in public spaces (streets, esplanades, etc.) it would help combat the phenomenon of urban heat islands.
Raw clay is a real alternative to high-carbon-footprint materials used for partitioning such as plaster and steel.
Is the construction sector taking advantage of these innovations and actually using these new materials?
CP-B: Companies are interested in these innovations, but the major obstacle lies in the lack of standards and regulations. The National TERRE Project is already working on good practice and on establishing recommendations ahead of those norms being formally codified. Public procurement has a role to play by promoting the use of such new materials to obtain valuable feedback. The commitment of all stakeholders - technical control offices, insurers, investors, and so on — is necessary to support projects that use new eco-materials. At the research level, the involvement of researchers in the human sciences is necessary to work on messaging and getting the general public to accept these new materials.
Materials that make the ecological transition
Durable, efficient, with a low carbon footprint... increasingly, used new materials come from natural products.
Biobased materials come from renewable organic matter (biomass), of animal or vegetable origin.
They can be as diverse as wood, straw, hemp, rice husk, corn cob, cork, sheep’s wool, reed, rapeseed, flax shives, duck feathers, and miscanthus.
Geo-based materials come from resources of mineral origin, such as raw earth or dry stone which have been used for millennia.
In respecting the logic of the circular economy, certain materials result from the reuse or recovery
of waste and by-products, such as cellulose wadding, recycled textiles, pallet wood, cardboard, or oyster shells.
You highlighted the role of a circular economy, based on the reuse and recycling of materials. How does this work on the ground?
CP-B: The signals are generally positive. The European Commission’s recent ‘circular economy package’ of 30 March 2022 aims to strengthen the requirements in this area. Several chairs on the circular economy in construction exist across Europe. But here too, industry norms are the main restricting factor. In addition, the recycling of waste in France needs further attention. With respect to concrete, the national Recybéton project has made progress by issuing recommendations for the use of recycled aggregates. Other sectors are also being created, as is the case with the straw sector in New Aquitaine.
LF: Making concrete with 100% recycled aggregates is a real challenge, as there are not enough resources to systematise this type of solution. The upstream sector (demolition companies, processors and waste collectors) also needs to be structured. In the Grand Est region, the Fibres-Energivie competitiveness cluster, dedicated to building materials, has taken on the challenge. It is necessary to federate the actors of the value chain and to organize them in order to adopt this approach more generally, making it possible to prolong the lifespan of materials resulting from demolition work. The circular economy is developing everywhere in Europe, such as in Switzerland where more and more construction players are implementing it.
1. Aquitaine Higher Institute of Building and Public Works, engineering school component of the University of Pau and Pays de l’Adour (UPPA).
2. Laboratory of engineering sciences applied to mechanics and electrical engineering.
3. https://fehrgroup.com/
4. The construction sector is responsible for more than 35% of the total waste produced in the European Union. Greenhouse gas emissions resulting from the extraction of materials, the manufacture of construction products, the construction and renovation of buildings are estimated to represent 5 to 12% of national emissions of these gases. A more efficient use of raw materials would avoid 80% of these emissions. (Source: European Commission, A new action plan for a circular economy, COM (2020) 98 final).
5. RE2020, which entered into force on 1st January 2022, aims to reduce CO2 emissions during construction, to make buildings less energy-consuming and to decarbonise the energy used by establishing emission ceilings. These will be increasingly restrictive, in three-year phases, by 2031.
6. “Decarbonising the cement-concrete sector”, The Shift Project, January 2022.
7. Geosourced, from resources of mineral origin, are for example raw earth or dry stone.
8. The inner part of the stem
9. Wool from the Manech sheep breed from the Basque Country.
10. International Union of Laboratories and Experts in Construction Materials, Systems and Structures.
11. Concrete is made up of sand, gravel, water and cement.
12. Clinker is a constituent of cement which results from the firing at 1,450°C of a mixture composed of around 75% limestone and 25% silica
Look further
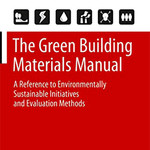
BOOK
The Green Building Materials Manual: A Reference to Environmentally Sustainable Initiatives and Evaluation Methods,
Hannah Rae Roth, Meghan Lewis, Liane Hancock, Ed. Springer, 2021.
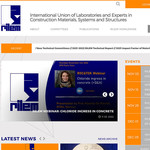
WEBSITES
RILEM - International Union of Laboratories and Experts in Construction Materials, Systems and Structures
https://www.rilem.net/
Unesco Chair - Earth:
https://terra.hypotheses.org/
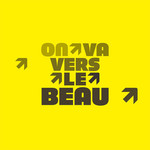
VIDEOS AND PODCASTS
Green building in Switzerland RTS podcast, 2020:
https://www.rts.ch/audio-podcast/2020/audio/eco-construction-2-5-de-nouveaux-materiaux-durables-font-leur-apparition-sur-les- chantiers-25152127.html
Sustainable bamboo houses by Elora Hardy in Bali, TED Conference
https://www.ted.com/talks/elora_ hardy_magical_houses_made_of_ bamboo
Today is already tomorrow
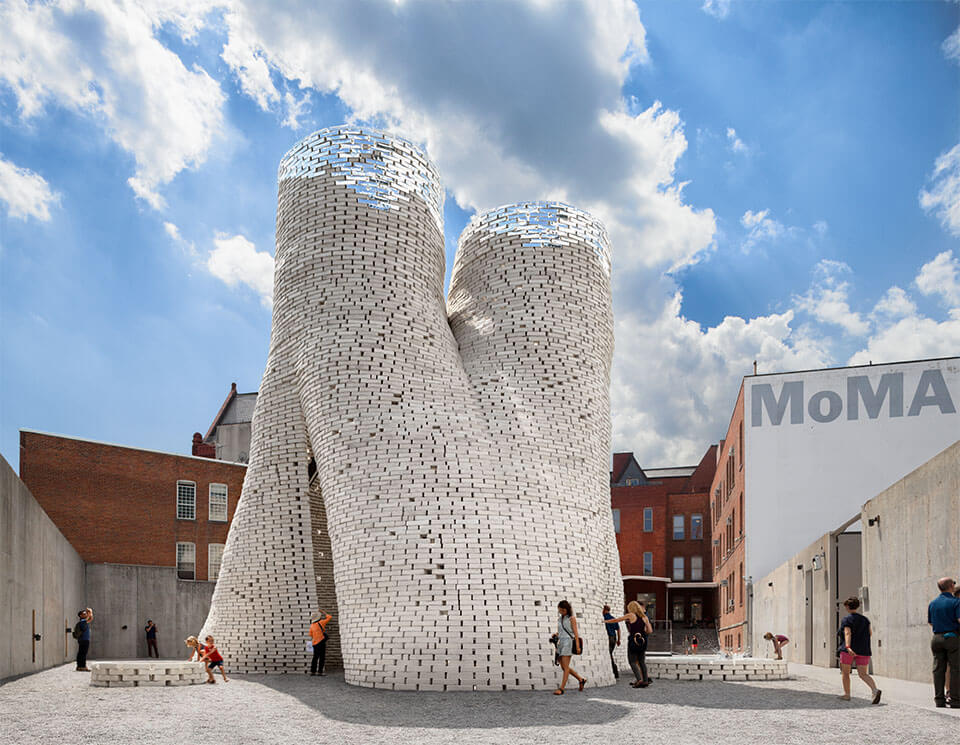
The mushroom house
Myco-architecture is no longer a Belgian comic book fiction! Research laboratories and companies are increasingly interested in the astonishing properties of mycelium, the roots of mushrooms, with which it is possible to manufacture solid, fire-resistant and highly insulating bio-bricks. As early as 2014, young architects exhibited Hy-Fi in the courtyard of the MoMA in New York, a 12-metre high tower made up of 10,000 myco-bricks. And NASA announced in early 2020 its plan to use this material to build the first human bases on the Moon and Mars.
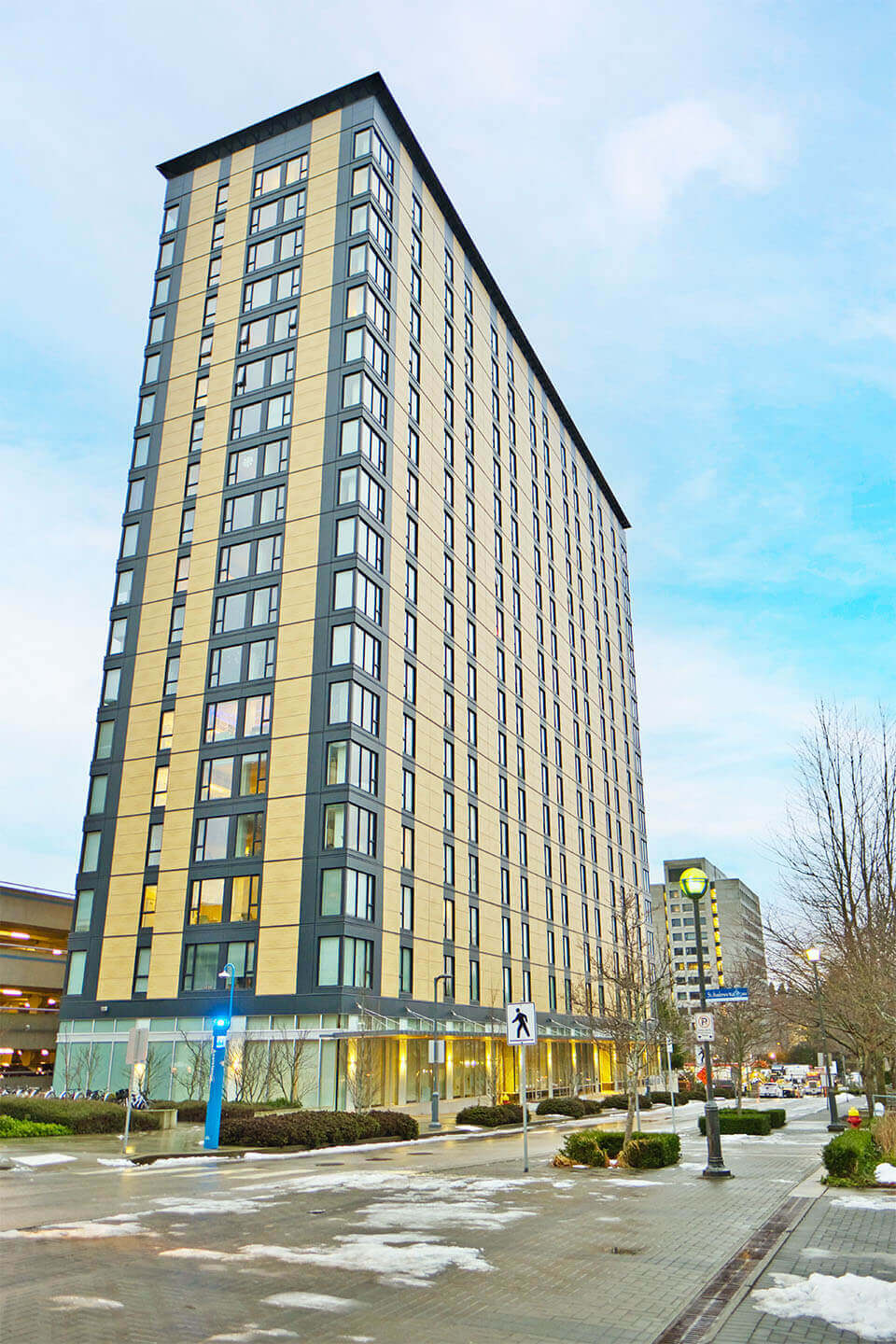
Wood is growing up
In Canada, the Green Building with Wood (CVBois) Program is funding tall wood building demonstration projects that focus on innovative solid wood timber products and systems.
The first of their kind are the Brock Commons Tallwood House student residence, an 18-storey building completed in 2017 on the campus of the University of British Columbia in Vancouver and Écocondos Origine, a 13-storey apartment building in Quebec City. As of 2021, the International Building Code in the United States now allows for the construction of tall wooden buildings up to 18 stories.
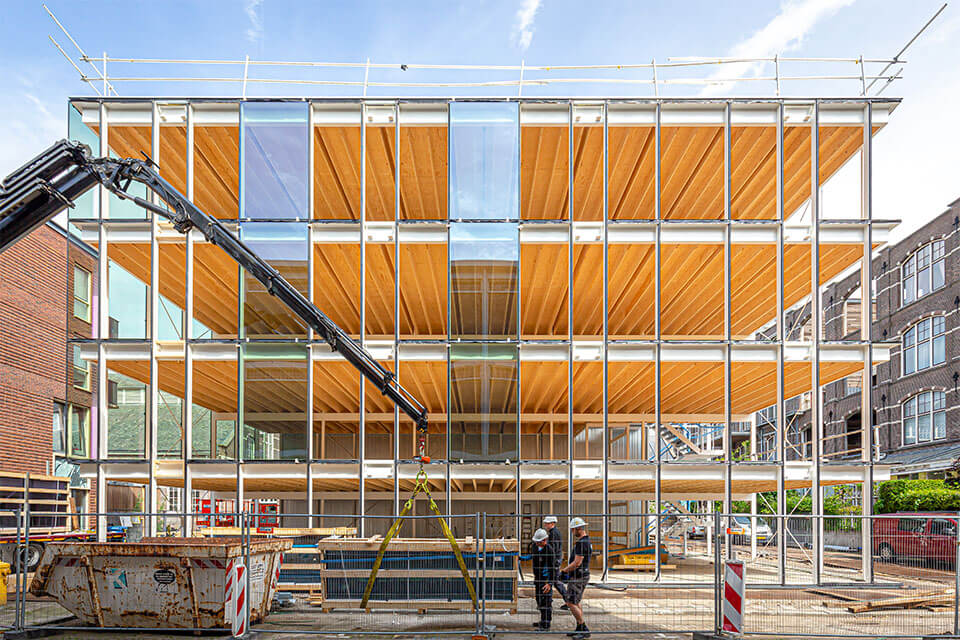
Material bank buildings
The circular economy is inspiring several new building projects across Europe. Examples are Building D in Delft in the Netherlands and the Nesto residences in Wilz in Luxembourg which have been built with total end-of-life recycling in mind. In Brussels, the BRIC (Build Reversible In Conception) project, a pilot initiative of the European BAMB (Buildings As Material Banks) project, is experimenting with the optimisation of materials use throughout building life-cycles. And the Dutch platform Madaster centralises information on the components that make up the buildings that are registered there, to facilitate their monitoring and reuse.
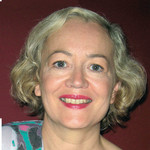
Text
Catherine Veglio
Editorial consultant, journalist, novelist, Catherine Véglio explores the fields of economy,
innovation, science, technology and their relationship with society.